Heat Press Machines
Why Insta?
Since 1959, Insta Graphic Systems has been the world’s leader in heat transfer technology
We pride ourselves on setting the standard for professional-grade heat press transfer machines, custom heat transfers and the interaction between these two products – the application process. The outcome is high-quality heat press graphics that last.
Insta heat press machines are equipped with superior pressure and temperature distribution across the entire platen AND recover heat significantly faster than other heat transfer machines on the market. This allows for consistent quality and faster production.
Insta machines are the most reliable and durable heat press machines available with an average useful life of 25+ years. Our heat presses continue to impress customers, earning us SGIA Product of the Year awards year after year.
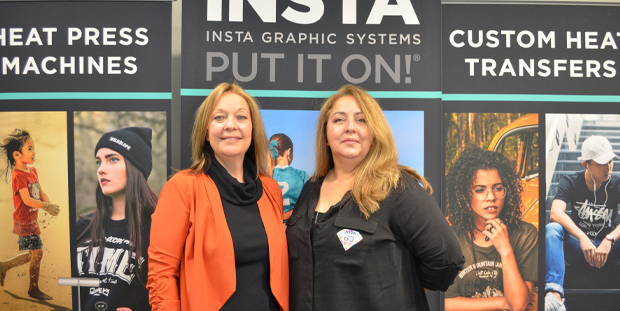
International
Insta is a global leader in heat transfer machine technology with over 45 years of international sales experience. We are represented through a network of distributors in over 125 countries around the world and maintain a European warehouse to facilitate the purchase and shipment of our professional-grade heat press machines overseas. Our multi-lingual staff is proficient in international shipping regulations, customs, and streamlining of the export process.
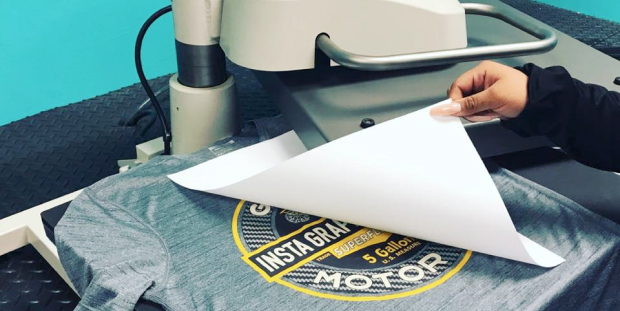
Safety & Warranty
All Insta machines proudly carry all regulatory safety agency approvals. Our heat press transfer machines are UL, ETL, CuL and CE approved and are RoHS/WEE compliant. These approvals ensure that our customers are purchasing machines that meet the highest regulatory standards.
Insta heat press machines are equipped with the following warranty:
- Lifetime on the upper heating element
- One year on parts
- 90 days on labor
What do I need for heat press machine?
To provide the versatility in printing and provide a long-lasting trouble-free life I recommend the accessory options listed below:
- Utility stand
- Interchangeable lower platens
- Teflon covers
- Maintenance kits
What do I need for a heat press machine?
The current global clothing and textile industry is worth an estimated $2.560 trillion. And if you want to make the decision to enter this market, then you’re going to need heat press machines or heat transfer presses to create your own designs. These machines are the foundation of a custom T-shirt business. However, if you want to make a mark in the industry, you’re going to need the right machine. For more information, see our article: Heat Presses: Why you need one and what to look for
What heat press machine to buy?
The worldwide clothing and textile industry, right now, is worth roughly $2.560 trillion. That’s crazy. It does, however, make sense. We all wear clothes every day, and therefore, we need to purchase clothing. If you are a part of this industry, you got into the right market. Being a business owner, especially in the clothing industry, is all about having the right tools. What is an essential tool that any clothing business should have, you ask? A heat press. Heat transfer presses allow customize-able designs to be printed on many different materials. You want one for your business, but you’re having trouble picking one. For more information, see our article: How to choose the right heat press for you Use your heat press to expand your customization capabilities
How does a heat press machine work?
Any machine that presses a transfer design onto a printable material is called a heat press. It uses high temperatures and pressures to permanently print the design onto a number of common items and materials. For more information, see our article: Answering common questions about heat transfer presses
How to choose a heat press machine?
When you’re running a production operation, you can’t risk equipment failure. You need the highest-quality, most reliable heat press machinery to maximize your profit and streamline operational efficiency. Check out these five tips for evaluating the quality of industrial heat presses and find the right fit for your business needs.
- Capabilities
- Size
- Style
- Temperature
- Quality
For more information, see our article: Five factors to consider when purchasing an industrial grade heat press