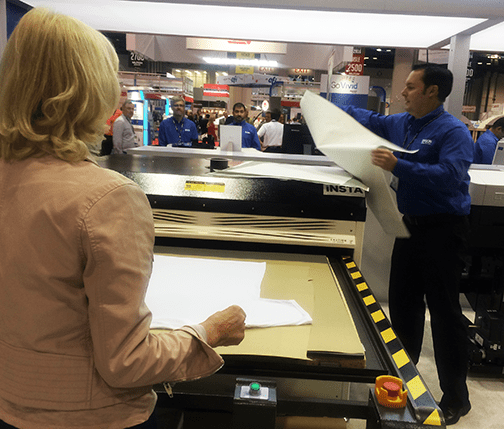
Printing News.com recently featured Insta in their Wide Format & Signage segment. As part of their “Fabric Printing Expert” series, they published an article covering sublimation heat printing and features interviews of Cris Saunders of Insta and Tim Check of Epson:
As our “Fabric Printing Expert” series draws to a close, we look at the last steps in the dye-sublimation-printed fabric production process: heat transfer and sewing.
Hot Hot Hot
An important piece of ancillary equipment for dye-sublimation printing is a heat press, also known as a “sublimator,” which admittedly sounds like something out of Star Trek. (“Guard! Throw him in the Sublimator!”) It’s tempting to think that all heat presses are the same, but that is far from true.
There are two basic configurations: roll-to-roll or rotary and flatbed. A roll-to-roll heat press, as you would expect, feeds the fabric from a roll. The fabric is sandwiched between the transfer paper on one side and often a protective paper on the other. The choice of roll-to-roll vs. flatbed will be determined by what it is you’re producing.
“Roll-to-roll heat presses are useful for doing long, continuous runs of fabric, such as patterns for apparel or long production runs of banners,” said Tim Check, Product Manager, Professional Imaging, at Epson. “If you know that you’re doing long lengths of jobs, like 10-foot banners or longer, a roll-to-roll heat press is pretty much the best way to produce that work.”
Flatbeds can offer more flexibility because they can also be used for rigid non-fabric materials like Chromolux that won’t go through a rotary press. Flatbeds are also less expensive and can take up less space than a roll-to-roll. It’s not uncommon for fabric printing shops to have a flatbed (or more than one) in addition to a roll-to-roll, if they need the versatility.
There is also a lot of work that could go on either device. “Jerseys, shirts, and even small signs and banners work well on a flatbed press,” said Check.
There are different varieties of both roll-to-roll and flatbed heat presses.
Roll-to-Rolls
Roll-to-roll heat presses differ in how they are heated.
In a roll-to-roll heat press, heat is produced in the central drum that the fabric and paper roll over. One type has a drum filled with oil that is heated to the optimal temperature required for sublimation (400°F). Another has electric heating elements mounted inside the drum. The advantage to an oil-filled drum is that it produces a more even and consistent heat around the circumference of the drum; in the oil-less presses, there can be slightly cooler gaps between the heating elements. If the heat is uneven across or around the drum during sublimation, there can be discoloration or other imperfections. Admittedly, though, fabric is a very forgiving substrate and small discolorations may not be noticeable, but buying an el cheapo heat press may cause more obvious problems. (A good oil-filled roll-to-roll heat press will run you about $30,000 to $60,000, but can last for 25 years or more. The electric ones run about $15,000 to $30,000. Cheaper ones can be found, but caveat emptor.) Oil-filled heat presses can also be more energy efficient as the oil can hold the heat for a long period of time. Different systems also have varying levels of automation.
Flatbeds
Unless you are doing long runs of continuous patterns for apparel or large volumes of signs, flags, and banners, a flatbed heat press will be the more practical option. Flatbeds also come in several varieties (bet you didn’t think there was this much nuance to heat presses):
- Clamshell, (such as Insta’s Model 158), which opens and closes like its molluscan namesake. Clamshell presses aren’t suited to thicker substrates like boards or pieces of wood because they won’t close fully and thus won’t heat the substrate evenly—or the edge opposite the hinge at all. For fabrics they’ll do fine.
- Swing-away, (such as Insta’s Model 828), on which the top part of the press slides to the left or right. When the fabric and transfer paper are positioned on the bottom platen, the top—with the heating element—slides over and the user pulls a lever to bring the two halves into contact. Swing-aways are the most common and popular.
- Drawer, (Insta’s new Model 1020 for example), which has a lower platen that can be pulled out from the front to load the material to be pressed. The drawer then slides back in place and the heating element is brought down on top of it.
Each one has its pluses and minuses, depending on what kind of materials you will be using it for.
(By the way, if you plan to use dye-sublimation transfer printing for things other than fabrics, such as mugs, plates, caps, and other 3D objects, you can purchase heat presses designed for these objects. A mug press for example is designed for cylindrical objects.)
Flatbed heat presses can be manual or automatic. Dye- sublimation transfer takes about 30 to 35 seconds, with slight variations based on the specific fabric, and manual presses chime or beep when that time is up and the user has to manually remove the heat from the substrate. Automatic presses will pop open when the time is up, making life a little easier if the user is operating more than one press or otherwise multitasking, as overheating can cause color problems.
There is a new variety of flatbed heat press called an “all over sublimation” heat press, which essentially “duplexes” dye-sub transfer. “There is a heating element on the top and the bottom,” said Check, “so if you want graphics on both sides of a T-shirt that are continuous and wrap around the shirt, it saves time and produces better quality graphics, since the paper and fabric stay aligned.”
Speaking of keeping paper and fabric aligned, as we saw in last month’s installment of this series, you may need to use a “tack” or sticky transfer paper on a flatbed press to prevent ghosting. “The only time you would need a tack paper for a rotary heat press is if the fabric you are sublimating to is very, very stretchy or there’s a lot of shrinkage with that fabric,” said Lily Hunter, Product Manager, Textiles and Consumables, for Roland. “Typically with most fabrics on a rotary heat press, you can go with non-tack.”
Dye-sublimation transfer is a function of heat, pressure, and time, and any variation in any of those elements can cause color shifts and other imperfections.
“When looking for a heat press, even temperature is probably the most important feature in a heat press,” said Cris Saunders, Director of Sales and Marketing for Insta Graphic Systems. Insta offers a variety of manual and automatic flatbed heat presses. “It is also important to consider design and materials that a heat press is made of.”
How well a heat press can maintain its temperature can be the difference between a 16 x 20-inch flatbed heat press that costs $300 and one that is closer to $2,000.
Sew What?
The final piece of the fabric printing puzzle is finishing, and for fabrics—be it soft signage or apparel—that often involves sewing, from basic hemming to keep the edges from fraying, to adding pole pockets or other elements to facilitate mounting.
The most important consideration when looking at sewing equipment—and the reason why you likely can’t use the Singer sewing machine you may have at home—is sheer horsepower. Some of the fabrics used for sign and display graphics are too thick for consumer-grade sewing equipment. Industrial grade sewing equipment is also faster, more rugged and durable, and offers a larger work area.
Shops producing apparel will often have two sewing devices: a normal sewing machine and a “serger,” or an “overlock sewing machine,” which creates an “overlock stitch” over the edges of two pieces of fabric, like the front and back of a shirt. A serger (the term comes from “serge,” a type of cloth) can also trim the edges of the cloth to create a clean seam in one pass.
There is a new finishing/mounting technique that is starting to appear in more and more places called silicon edge graphics (SEG). Essentially, a thin silicon strip is sewn around the edge of the graphic, which slots into a groove in a thin aluminum frame. The print needs to be sized precisely so that the fabric remains taught when installed in the frame, but the effect is reminiscent of rigid panel display graphics. “You can use it for regular fabric displays, but also for backlit fabric displays,” said Check, “by adding a little LED lightstrip around the inside of the frame.” SEG is showing up in airports and other public spaces. “They’re moving away from backlit films and display boxes,” said Check. “[SEG] has a more vibrant appearance, and it also absorbs sound.”
Sewing It All Up
When looking for heat presses, sewing machines, or any other post-printing equipment, there are, as you have seen, many many options that can seem a but overwhelming. The decision, though, doesn’t have to be a complicated one.
“Choose what fits for the majority of your work,” advised Check.
“Do your homework before making a heat press decision,” said Saunders. “Find a press that has the key elements for quality and reliability while evaluating what it will be used for to ensure you get the right model to suit your specific needs.”